Advancements & Trends in Concrete Technology for Meeting Sustainability Demand
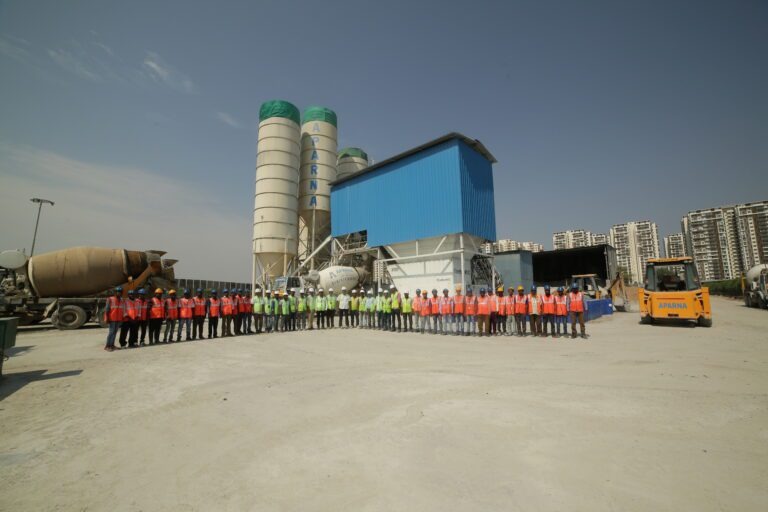
June 14, 2024
An exclusive interview with Mr. Gopal Krishna, Business Head, Aparna RMC
The construction industry is rapidly evolving, driven by the urgent need for sustainable solutions. With urbanization and infrastructure development on the rise, there’s a growing demand for concrete that meets structural requirements while minimizing environmental impact. Innovations in concrete technology are focused on sustainability, incorporating recycled materials, reducing carbon emissions, and optimizing production processes. Aparna Enterprises Ltd (AEL), known for its wide spectrum of building-material products, is at the forefront of this transformation.
Constrofacilitator recently interviewed Mr. Gopal Krishna, the Business Head of Aparna RMC. With over 21 years of experience, he has been instrumental in driving sustainable and profitable growth in the construction segment, particularly in cement and ready-mix concrete (RMC). His expertise has led to significant business expansion and the successful implementation of advanced ERP/SAP projects.
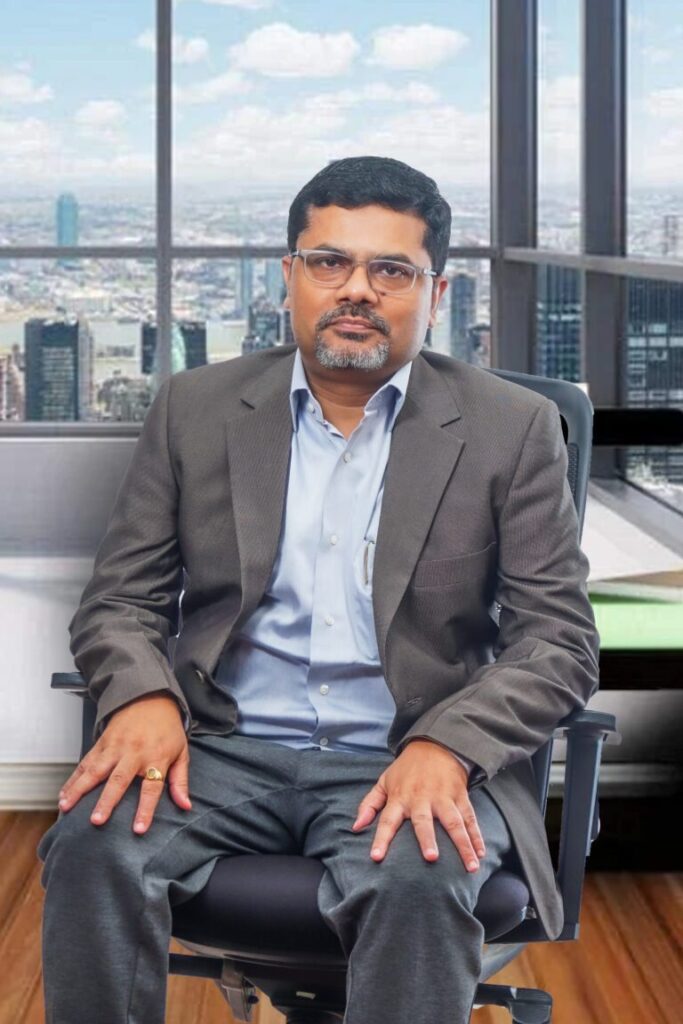
Mr. Gopal Krishna,
Business Head, Aparna RMC
Upcoming Trends and Innovations in Concrete Construction
Mr. Krishna foresees a dramatic transition in the concrete construction industry, driven by technological advancements, better materials, and modern construction methods. The future is focused on sustainability. Traditional concrete production is responsible for about 8% of global CO2 emissions, but the advent of ‘Green Concrete’ aims to reduce this impact by utilizing recyclable materials, producing less carbon dioxide, and consuming less energy. This results in more durable and economical concrete.
Another innovation is Smart Dynamic Concrete (SDC), which significantly reduces the carbon footprint of the construction process through lower cement content and reduced energy consumption. SDC offers faster concrete placement, higher durability, and better ecological performance.
Additionally, technologies like drones and 3D printing are transforming concrete construction. Drones are used for site inspections, progress monitoring, and data collection, while 3D printing allows for the creation of sophisticated concrete structures with a shorter turnaround time.
Making Cement Production Environmentally Sustainable
Several initiatives are enhancing the sustainability of cement production. Carbon Capture and Storage (CCS) technology is a key innovation, capturing CO2 emissions during cement production and repurposing it as a concrete additive. This approach significantly reduces greenhouse gas emissions.
Green concrete and smart dynamic cement are also gaining prominence. These materials incorporate recycled industrial by-products like fly ash and slag, improving concrete performance and reducing environmental impact. Furthermore, substituting traditional fuels with Refused Derived Fuels (RDFs) and increasing the use of Sewage Sludge (SS) in cement production have shown substantial reductions in CO2 emissions.
Quality Control in Concrete Production
Aparna RMC ensures stringent quality control measures throughout the production process. Their 27 plants are computerized with MCI 360 and Siemens PLCs, guaranteeing accurate batching and continuous production. Custom mixes of aggregates, cement, and admixtures are created to meet specific project requirements. This meticulous approach ensures that the concrete supplied is of high quality and meets industry standards.
Recent Innovations Influencing Concrete Performance
Innovations in cement technology are continuously improving concrete performance and reducing its environmental impact. Research shows that substituting coal with RDFs can save significant amounts of coal and reduce CO2 emissions. Using alternative cementitious materials like fly ash, slag, and other industrial by-products also helps mitigate the environmental effects of cement production.
Carbon capture technology is another significant innovation. Capturing CO2 emissions during cement production and using it in concrete production can drastically reduce greenhouse gas emissions. Recycled aggregates and other environmentally friendly additives are also being explored to enhance concrete performance and sustainability.
Incorporating Sustainable Practices
Aparna RMC is committed to sustainability. They incorporate recycled aggregates and supplementary cementitious materials (SCMs) like fly ash and slag into their concrete production. Their controlled batch process minimizes wastage and conserves resources. Additionally, their water management strategy involves reducing consumption and recycling water to limit environmental impact.
Ensuring Quality and Consistency in Ready-Mix Concrete
Maintaining high-quality concrete requires adherence to several key principles. Proper mixing ensures a homogeneous blend of cement, aggregates, water, and admixtures. The water-to-cement ratio must be consistent, as too much water weakens the concrete while too little makes it difficult to work with. The dimensions and quality of aggregates also impact the mix, with fine aggregates needing to absorb more water for better workability. Using only the highest quality cement and aggregates ensures the best outcomes. Sustainable approaches, such as using recycled aggregates and SCMs, not only reduce the environmental burden but also improve the quality of ready-mix concrete.
Conclusion
Aparna RMC is leading the way in sustainable concrete technology, driven by innovation and a commitment to quality. By incorporating advanced materials and cutting-edge technologies, they are setting new standards in the construction industry, ensuring that future developments are both environmentally friendly and structurally sound.
Click to learn more about the future of concrete, sustainable solutions and innovative technologies.