Concreting in Hot Weather Conditions: How to Avoid the Problems That It Presents
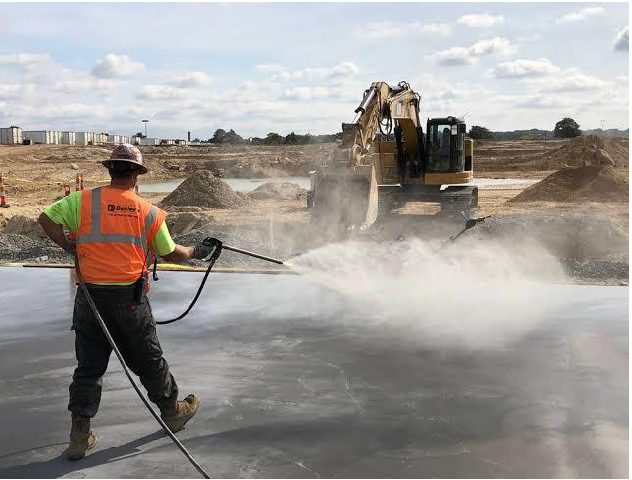
June 30, 2024
Hot weather poses significant challenges for concreting, potentially affecting the quality, durability, and strength of the finished product. High temperatures, low humidity, and increased wind speeds can accelerate the rate of evaporation of water from the concrete mix, leading to various issues such as rapid setting, reduced workability, and increased risk of cracking. Understanding these challenges and employing effective strategies to tackle them is crucial for achieving successful outcomes in hot weather concreting. Let us understand some of the challenges briefly
Challenges of Hot Weather Concreting
1. Accelerated Setting Time: High temperatures speed up the hydration process, causing the concrete to set faster than normal. This reduced working time makes it a problem to lag the concrete in proper time. It can make it difficult to properly place, consolidate, and finish the concrete which will result in all kinds of problems.
2. Increased Water Demand: Hot weather leads to rapid evaporation of water from the concrete surface. This makes the pour dry. It can be tackled by an increased amount of water in the mix, potentially compromising the water-cement ratio which in turn may decrease the resulting strength of the concrete. Increased water demand also makes your construction less sustainable.
3. Plastic Shrinkage Cracking: Quick evaporation can cause plastic shrinkage cracks to form on the surface of the concrete while it is still in its plastic state. These cracks occur when the surface moisture evaporates faster than it can be replenished by the bleeding process, leading to a rapid reduction in volume while the concrete is still in its plastic state. This phenomenon typically happens within the first few hours after placing the concrete and can compromise both the aesthetics and integrity of the finished product.
4. Thermal Cracking: In hot weather conditions due to pervasive heat and high temperature of pours, large temperature differences occur within the concrete, caused by rapid cooling on the surface and slower internal cooling. This leads to cracks in the building affecting its strength and aesthetical beauty.
5. Decreased Long-Term Strength: Improper concrete curing due to hot weather conditions can result in inadequate hydration, affecting the long-term strength and durability of the concrete.
6. Porous Concrete: Incomplete hydration and rapid drying can lead to a more porous concrete structure. Higher porosity means more voids within the concrete, which reduces its overall strength and makes it more susceptible to freeze-thaw cycles and chemical attacks.
7. Lower Density: A porous structure also implies a lower density, which directly correlates with reduced compressive strength.
Strategies to Mitigate Hot Weather Concreting Problems
1. Planning and Scheduling: Plan concreting activities during cooler parts of the day, such as early morning or late evening. Avoiding the peak heat hours can significantly reduce the adverse effects of high temperatures. So avoiding the afternoon for laying concrete and using it for other purposes will make concreting efficient.
2. Use of Admixtures: In summer using admixture to retain moisture, reduce setting time, etc can help you concrete better. Admixtures such as retarders can be used in the concrete mix to slow down the setting time, giving more time for proper placement and finishing of the pour. Water-reducing admixtures can also help maintain workability without compromising strength. Ready-mix suppliers can adjust the concrete mix design by incorporating admixtures specifically formulated for hot weather conditions. These admixtures can improve workability, reduce setting time, and enhance overall concrete performance in high temperatures.
3. Cooling the Ingredients: Use chilled water or ice as part of the mixing water to lower the temperature of the concrete mix. Additionally, cooling the aggregates by shading or sprinkling with water can help reduce the overall mix temperature. Storing the ingredients in a cold and shaded place to maintain lower temperatures can be a sustainable measure. Ready-mix concrete is typically mixed and transported in specialized equipment that can help control the temperature of the concrete mix. Cooling systems can be integrated into batching plants to lower the temperature of ingredients before mixing.
4. Moisture Retention: Moisture retention becomes a pressing issue in hot weather concreting. So usage of fog sprays, evaporation retarders, or wet coverings to keep the surface of the concrete moist and reduce the rate of evaporation can be beneficial. This is particularly important immediately after placement and during the initial concrete curing period.
5. Proper Concrete Curing Techniques: Implement effective curing methods such as Ponding by creating a water pond on the surface of the concrete (ponding is effective but not practical for large sites). Other techniques such as sprinkling or fogging where continuous spraying of water is maintained to retain moisture. Use of concrete curing compounds, or wet coverings (such as burlap) to maintain adequate moisture levels in the concrete can also be done. Ready-Mix concrete is produced in controlled environments which aids in the workability of the concrete during the curing process.
6. Rapid Placement and Finishing: Organize the work efficiently to ensure that concrete is placed and finished as quickly as possible. This may involve increasing the workforce or using additional equipment because any delay in the placement and finishing of the product can hamper your building’s aesthetic as well as structural integrity. RMC is useful in saving time here as it doesn’t require extra manpower and is ready-made to quickly place and finish the product.
7. Controlled Production Environment: Ready-mix concrete is produced in controlled batching plants, which allows for precise measurement and control of ingredients such as aggregates, cement, water, and admixtures. This ensures consistency in quality and performance, especially crucial in hot weather conditions where variations in mix proportions can significantly affect concrete properties.
8. Wind Barriers and Sunshades: Erect windbreaks and sunshades around the work area to reduce the effects of wind and direct sunlight on the concrete surface. It will help retain moisture because of less amount of direct sunlight falling on the building, it will increase workability and give more time for placement, finishing and curing of the concrete. It can also ensure a uniform curing throughout the building. Canopies, tents, tarpaulins, mesh screens, temporary walls, or natural shades can be used for the purpose.
Conclusion
Concreting in hot weather conditions requires careful planning, preparation, and execution to prevent the problems associated with high temperatures. Using Aparna RMC lets you adopt appropriate measures such as adjusting the mix design, using admixtures, cooling ingredients, maintaining moisture, and ensuring proper curing. Aparna RMC produces high-quality concrete even under challenging environmental conditions through its planned batching, controlled production environment, and unwavering commitment to providing the best even in stringent conditions. We at Aparna RMC understand the specific needs of your project and apply these strategies to help ensure the structural integrity and longevity of the concrete, regardless of the weather.