Temperature Control Concrete: Managing Thermal Stress in Large Structures
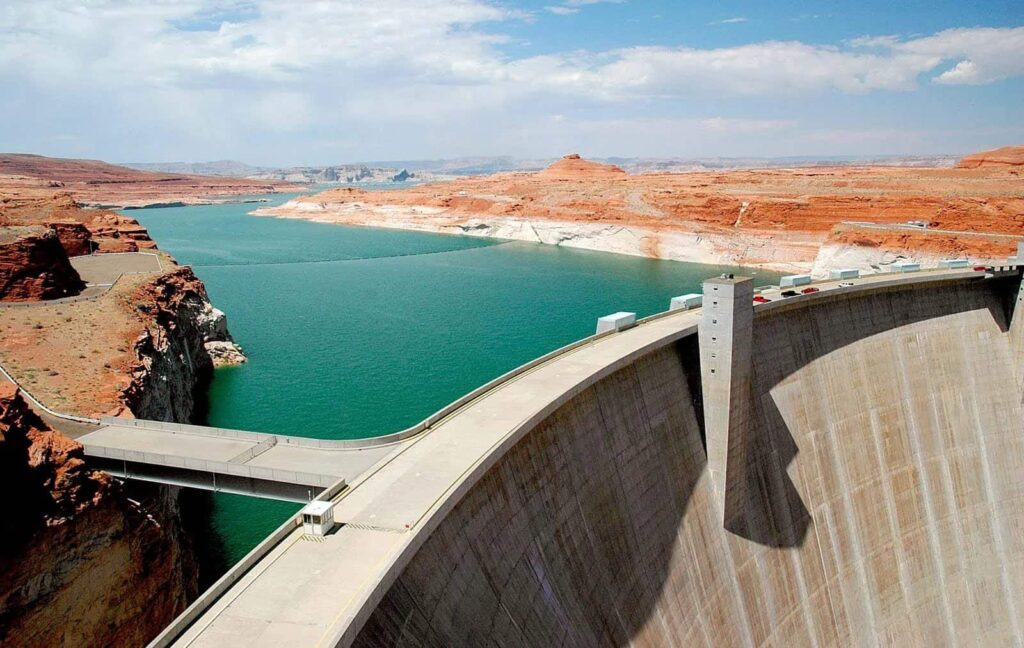
November 23, 2024
When constructing large structures such as dams, bridges, or high-rise buildings, managing thermal stress becomes crucial. One of the most effective methods to address this challenge is through temperature control concrete. This specialized approach minimizes the risk of cracking and structural instability caused by temperature fluctuations during concrete curing.
In this article, we will delve into the importance of temperature control concrete, its benefits, and practical strategies for managing thermal stress in large-scale construction projects.
I. Understanding Thermal Stress in Concrete
Concrete generates heat during the curing process due to a chemical reaction called hydration. In large concrete pours, the core temperature may rise significantly higher than the outer surface. This temperature difference causes internal thermal stress, which can result in cracking, reducing the durability and strength of the structure.
II. The Role of Temperature Control in Large Structures
In massive concrete pours, the stakes are high. Cracking not only compromises the structural integrity but can also lead to costly repairs and long-term maintenance issues. Temperature control concrete is designed to regulate heat generation and dissipate excess heat, ensuring a uniform temperature throughout the structure.
III. Key Benefits:
- Enhanced Structural Integrity: Prevents cracking caused by thermal stress, extending the lifespan of the structure.
- Improved Aesthetic Quality: Reduces surface imperfections such as shrinkage cracks.
- Cost Savings: Minimizes repair needs, delays, and material wastage.
IV. Techniques for Temperature Control in Concrete
Various strategies and technologies can help manage thermal stress in concrete pours. Here are some widely used methods:
1. Pre-Cooling
- Why It Works: Lowering the temperature of raw materials such as water, aggregates, and cement before mixing reduces the initial heat generated during hydration.
- How It’s Done: Chilled water or ice is used during the mixing process, and aggregates may be cooled using liquid nitrogen.
2. Post-Cooling
- Why It Works: Internal cooling pipes are embedded within the concrete structure to circulate chilled water, dissipating excess heat from the core outward.
- How It’s Done: Cooling systems remain operational until the concrete reaches a safe and stable temperature.
3. Surface Insulation
- Why It Works: Protecting the outer surface of the structure minimizes rapid cooling or heating due to environmental factors.
- How It’s Done: Insulating blankets or curing compounds are applied to regulate temperature differences between the surface and the core.
4. Using Low-Heat Cement
- Why It Works: Low-heat cement releases heat more gradually during the hydration process, reducing the risk of thermal stress.
- How It’s Done: Selecting specific cement blends tailored to large pours ensures a controlled curing process.
5. Optimizing Mix Design
- Why It Works: Adjusting the proportions of cementitious materials, water, and aggregates can influence the heat generated during hydration.
- How It’s Done: Using supplementary cementitious materials (SCMs) like fly ash or slag decreases the heat of hydration.
V. Best Practices for Effective Implementation
- Thermal Monitoring: Use temperature sensors to track core and surface temperatures in real-time.
- Gradual Cooling: Avoid rapid cooling to prevent thermal shock.
- Collaborative Planning: Engage structural engineers, concrete suppliers, and contractors early in the design phase to optimize temperature control measures.
VI. Introducing TempCrete by Aparna RMC
To address the challenges of temperature management in extreme conditions, Aparna RMC developed TempCrete, a specialized concrete designed to withstand temperature fluctuations. This innovative solution ensures optimal performance and durability, even in the most demanding environments.
Conclusion
Managing thermal stress in large structures is vital for ensuring long-term durability and performance. Temperature control concrete offers an effective solution by minimizing the risks associated with thermal cracking. By adopting techniques such as pre-cooling, post-cooling, and optimized mix designs, construction professionals can confidently tackle the challenges of large-scale concrete pours.
Implementing temperature control measures not only safeguards the structural integrity of a project but also contributes to cost efficiency and sustainability. As construction technologies continue to evolve, temperature control concrete will remain a cornerstone of modern engineering excellence.